Nitronic® 60
Nitronic® 60 - Gall-Tough® Plus - HPA N60 - UNS S21800 - Alloy 218 - N60 Steel - Material P513 - N & Mn Strengthened Stainless Steel
Home > All Alloys > Nitronic® 60
Level 6 is noted by its minimum ultimate tensile strength of 230 Ksi. By cold working our materials, we retain better elongation values through grain structure improvements that reduce the brittleness often associated with high strength materials. While our level 6 is primarily offered for alloys N50 and N60, we also cold work alloy C276, and are willing to try research for your high-performing alloy requirements.
For more information, check out our popular high strength options N60 HS and N50 HS.
N60 is truly an all purpose stainless steel alloy that exhibits remarkable versatility. HPA stocks varying degrees of melt qualities from AOD (Argon Oxygen Decarburization) to aerospace quality ESR (Electro-Slag Remelting ). This fully austenitic alloy was originally designed as a high temperature alloy, and subsequently has good high temperature properties for temperatures around 1800 ºF. The oxidation resistance of N60 is similar to Type 309 S.S., and far superior to Type 304 S.S.. However, its standout characteristic lies in its exceptional wear and galling resistance.
Nitronic® 60 is a Nitrogen-strengthened stainless steel that provides a significantly lower cost way to fight wear and galling when compared with alloys high in Cobalt or Nickel which are often used in bearings. Its uniform corrosion resistance is better than Type 304 in most media. Its chloride pitting resistance is superior to Type 316. Room temperature yield strength is nearly twice that of Types 304 and 316. In addition, N60 stainless steel provides excellent high-temperature oxidation resistance and low-temperature impact resistance.
The addition of elevated Silicon levels, even compared to the other Nitronic grades, helps to make N60 one of the greatest value wear alloys with superb non-galling and anti-seizing properties. This all purpose alloy is even better in cold worked, high strength. While you may be familiar with draw bench cold work, at HPA we use GFM rotary forges to achieve superior results with larger diameters than wire. In the table below, you can see our high strength N60 mechanical properties from our cold working process.
For more information on High Strength N60, please see our N60 HS page.
Cold Worked High Strength N60 Table | ||||
---|---|---|---|---|
HPA's Strength Spec. | Ultimate Tensile Strength Min. Ksi (MPa) | 0.2% OS Yield Strength Min. Ksi (MPa) | Elong. 4D Min. % | Reduced Area Min. % |
Level 1 HPA-MS-101 | 110 (758) | 90 (620) | 35 | 55 |
Level 2 HPA-MS-102 | 135 (930) | 105 (724) | 20 | 50 |
Level 3 HPA-MS-103 | 160 (1103) | 130 (896) | 15 | 45 |
Level 4 HPA-MS-104 | 180 (1241) | 145 (999) | 12 | 45 |
Level 5 HPA-MS-105 | 200 (1379) | 180 (1241) | 10 | 45 |
UTS = Ultimate Tensile Strength, YS = Yield Strength, OS = Offset
Typical annealed mechanical properties here.
Datasheet
View or download our Nitronic 60 datasheet here
Chemistry*
Min% | Max% | |
---|---|---|
Fe | Bal. | |
Cr | 16.0 | 17.0 |
Ni | 8.00 | 8.50 |
Si | 3.70 | 4.20 |
Mn | 7.50 | 8.50 |
N | 0.10 | 0.18 |
C | 0.060 | 0.080 |
P | 0.040 | |
S | 0.030 | |
Mo | 0.75 | |
Cu | 0.75 | |
Ti | 0.050 | |
Al | 0.020 | |
B | 0.0015 | |
Nb | 0.10 | |
Sn | 0.050 | |
V | 0.20 | |
W | 0.15 |
Typical Inventory
Round Bar, Flat Bar, Hex Bar, Square Bar, Wire Spool, Tig Wire, Loose Coil, Wire Reel, Plate, Strip, Coil, Hot Band, Tubing, Fastener, Machined, Forge, Billet, Rcs
We've expanded our in-house capabilities in:
For more information, you can contact us at 1-800-472-5569, and request our sales department. You can also view our brochure online! There's also more information about our offered services on our production services page.
Applications
- Actuators - capable even in cryo temperartures needed in deep space
- Orthodontics & Surgical equipment - excellent corrosion resistance and non-galling properties
- Automotive valves - can withstand gas temperatures of up to 1500 °F for a minimum of 50,000 miles.
- Fastener galling - capable of frequent assembly and disassembly, allowing more use of the fastener before the threads are torn up, also helps to eliminate corroded or 'frozen' fasteners.
- Pins - Used in roller prosthetics & chains to ensure a better fit of parts (closer tolerance, non-lubricated) and longer lasting.
- Marine shafts - better corrosion than types 304 and 316 with double the yield strength.
- Pin and hanger expansion joints for bridges - better corrosion, galling-resistance, low temperature toughness, & high charpy values at sub-zero temps compared to the A36 and A588 carbon steels commonly used.
General Data
The additions of Silicon and Manganese have given this alloy a matrix to inhibit wear, galling, and fretting even in the annealed condition. Higher strengths are attainable through cold working the material and is still fully austenitic after severe cold-working. This working does not enhance the anti-galling properties as is normal for carbon steels and some stainless steels. The benefit to the cold or hot work put into the material is added strength and hardness, and the wear resistance does not decrease noticeably. Chromium and Nickel additions give it comparable corrosion to 304 and 316 stainless steels, while having approximately twice the yield strength. The high mechanical strength in annealed parts permits use of reduced cross sections for weight and cost reductions through the use of thinner stock.
If your galling problem occurs at less than 1500 ºF, then you should consider switching to this alloy. N60 has a better value and cost advantage than any other alloys available. Whereas other materials require an additional amount of heat treating to raise their hardness, N60 is excellent in the annealed condition and is available cold worked at HPA. Cold working refines the grain structure for high strength properties and allows for better elongations, less brittleness.
- Fights galling and wear stronger than 304 / 316 SS.
- Outstanding galling resistance at both ambient and elevated temperatures.
- A very strong option for valve stems, seats, trim, fastening systems including nuts and bolts, screening, chain-driven systems, pins, bushings and roller bearings, and pump components such as wear rings and lobes.
- Most effective wear and galling resistant alloy for bridge pins and other critical construction applications.
Mechanical Properties
The typical properties listed can usually be provided in rounds, sheet, strip, plate, & custom forgings. We have the equipment to produce small quantities in special sizes to meet our customers’ specific needs. The table below shows Electralloy's Typical Room Temperature Tensile [Mechanical] Properties* of Nitronic® 60 Stainless Steel. For most common forms and exceptions, check out the datasheet linked underneath the table.
Size inch (mm) | Cond. | UTS ksi (MPa) | YS ksi (MPa) | Elong. % in 4XD | Reduced Area % | Rockwell Hardness |
---|---|---|---|---|---|---|
1” (25.4) Ø | Anneal | 103 (710) | 60 (414) | 64 | 74 | 95B |
1-3/4” (44.4) Ø | Anneal | 101 (696) | 56 (386) | 62 | 73 | 100B |
2-1/4” (57.2) Ø | Anneal | 101 (696) | 60 (414) | 60 | 76 | 100B |
3” (76.2) Ø | Anneal | 113 (779) | 65 (448) | 55 | 67 | 97B |
4-1/8” (104.8) Ø | Anneal | 106 (731) | 56 (386) | 57 | 67 | 95B |
1/2"Ø & <1/2” (12.7)Ø | AMS 5848 | 105 min. (724) | 55 min. (379) | 35 | 55 | 170-255 HB** |
>1/2” (12.7)Ø | AMS 5848 | 95 min. (655) | 50 min. (344) | 35 | 55 | 170-255 HB** |
UTS = Ultimate Tensile Strength, YS = Yield Strength
*Data based on duplicate tests
**Data based on bars, please see spec. or call for more information
Cold Worked High Strength N60 Table | ||||
---|---|---|---|---|
HPA's Strength Spec. | Ultimate Tensile Strength Min. Ksi (MPa) | 0.2% OS Yield Strength Min. Ksi (MPa) | Elong. 4xD Min. % | Reduced Area Min. % |
Level 1 HPA-MS-101 | 110 (758) | 90 (620) | 35 | 55 |
Level 2 HPA-MS-102 | 135 (930) | 105 (724) | 20 | 50 |
Level 3 HPA-MS-103 | 160 (1103) | 130 (896) | 15 | 45 |
Level 4 HPA-MS-104 | 180 (1241) | 145 (999) | 12 | 45 |
Level 5 HPA-MS-105 | 200 (1379) | 180 (1241) | 10 | 45 |
UTS = Ultimate Tensile Strength, YS = Yield Strength, OS = Offset
Common Specifications
Note that the specifications listed are common for this alloy but are for reference only and may be specific to a certain form. The specifications listed are not comprehensive nor indicative of any edition, revision, or similar such as an amendment. Please, reach out to our sales department to request the Material Test Report (MTR) or to confirm your required specifications.
Form | Standard Specification |
---|---|
Identification | UNS S21800 |
Bar | AMS 5848, ASTM A276, ASME SA276 |
Cold Worked Bar | HPA MS: 101, 102, 103, 104, 105 (properties here) |
Wire Coil | ASTM A580 |
Sheet, Plate, or Strip | ASTM A240, ASME SA240 |
Boilers and Pressure Vessels | ASTM A479, ASME SA479 |
Fasteners | ASTM A193 Grade B8S Class 1C, ASTM A194 |
Forging | ASTM A314, AMS 5848 |
Weld Wire | N60W/ UNS S21880/ AWS A5.9 Class ER218 |
Billet | ASTM A314 |
Medical | ASTM F899 |
Others | NACE MR-0175, ISO 15156 |
Galling Resistance
Galling is the tearing of metal surfaces which suddenly renders a component unserviceable. Galling is a major concern in two areas of application in particular – threaded assemblies and valve trim. A button and block galling test is commonly used to rank alloys for their galling tendencies. In the test procedure, a dead-lead weight is applied in a floor model Brinell Hardness Tester on two flat polished surfaces (10-20 microinches). The 0.5 inch (12.7 mm) diameter button is slowly rotated by hand 360 under the load and then examined for galling at a 7X magnification. If galling has not occurred, new specimens are tested at higher stresses until galling is observed. The threshold galling stress is selected as the stress midway between the highest nongalled stress and the stress where galling was first observed. Results are reproducible within +/- 2.5 ksi (18 MPa). However, this test should not be used for design purposes because of the many unknown variables in a particular application. The test has proven highly successful as a method of screening alloys for prototype service evaluation.
Elevated Temperature Galling Applications
N60 stainless steel has performed successfully in elevated temperature service for valve trim. Several austenitic stainless streels were evaluated as stems and bushings in an automotive emissions control butterfly valve. However, only N60 operated smoothly over the entire temperature range. The other alloys galled in the 800-1500 °F (427-816 °C) temperature range. Another application involved a 20-inch (508 mm) gate valve which opened and closed every 170 seconds at 750 °F (399 °C). N60 weld overlays on the seat and disk lasted 140 days without galling which would have quickly contaminated the process. A similar valve with Stellite® 6B hard faced trim lasted only 90 days.
Wear Resistance
Data shown in figure 1 was developed under the following test conditions: Taber Met-Abrader machine, 0.500 inch (12.7 mm) crossed 90 degrees cylinders, no lubricant, 16 pound (71 N) load, 105 RPM (and 415 RPM where noted), room temperature, 120 grit surface finish, 10,000 cycles, degreased in acetone, duplicate tests, weight loss corrected for density differences.
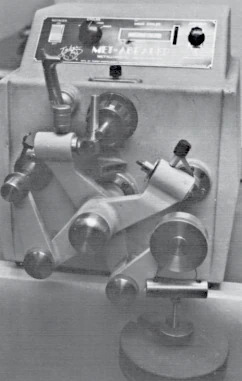
Wear of Heat Treatable Steels
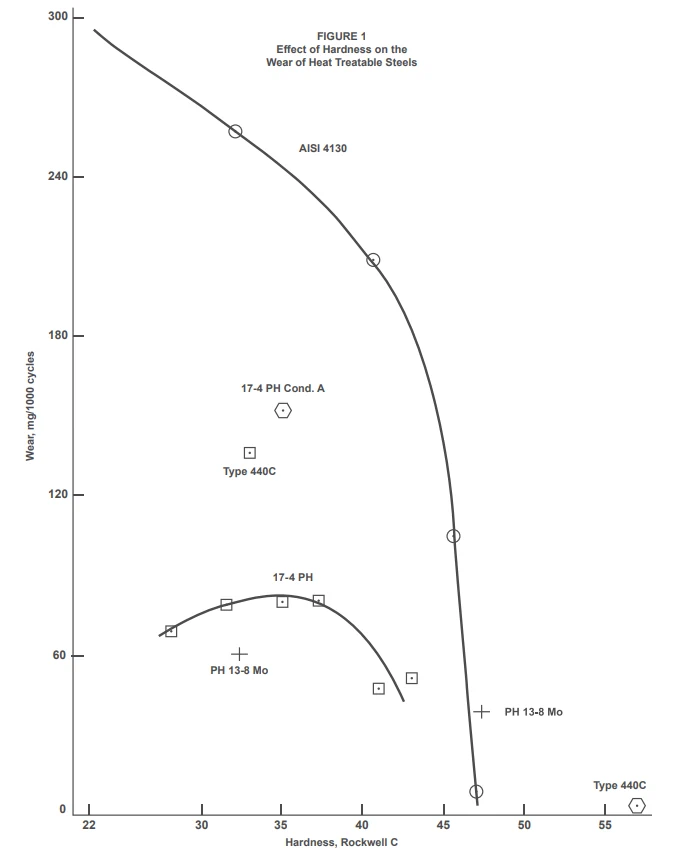
N60 and Stellite 6B
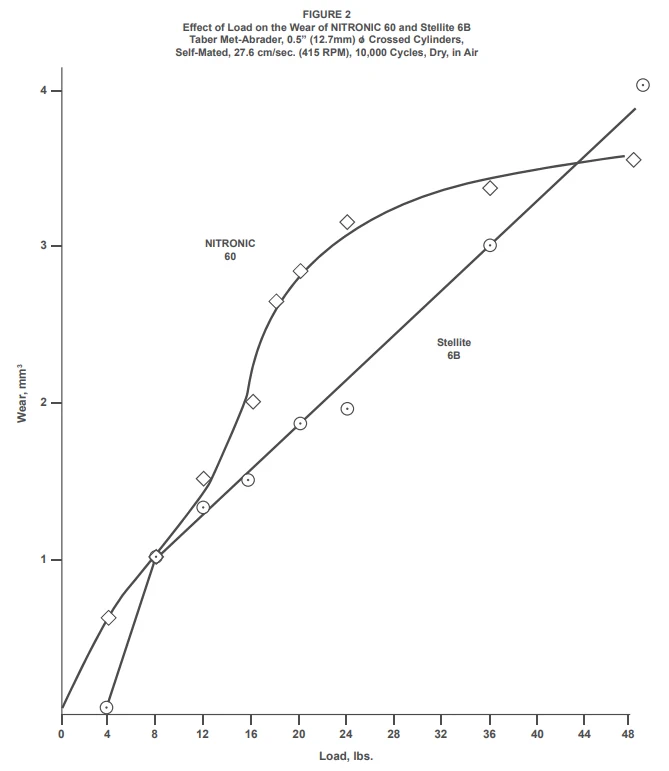
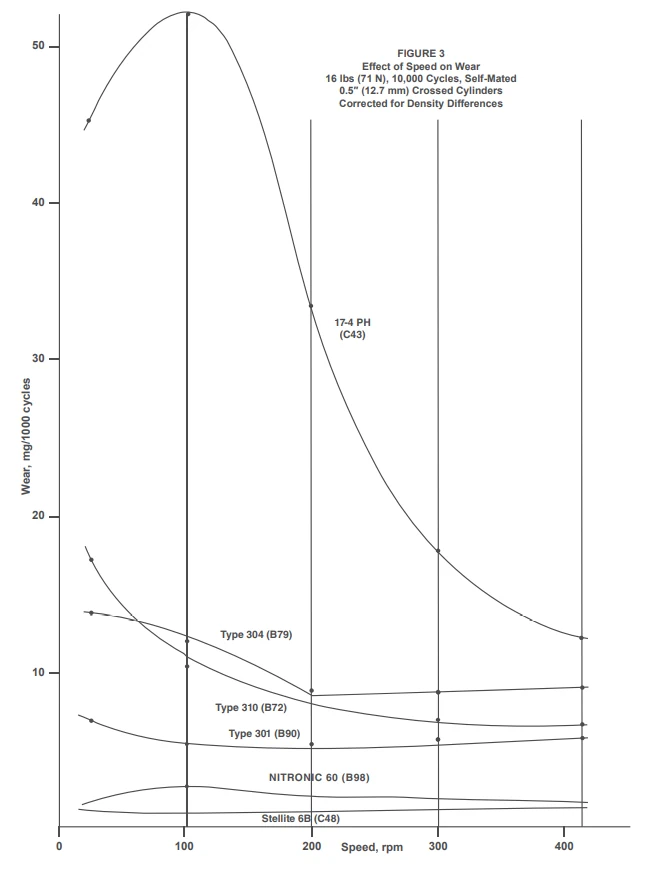
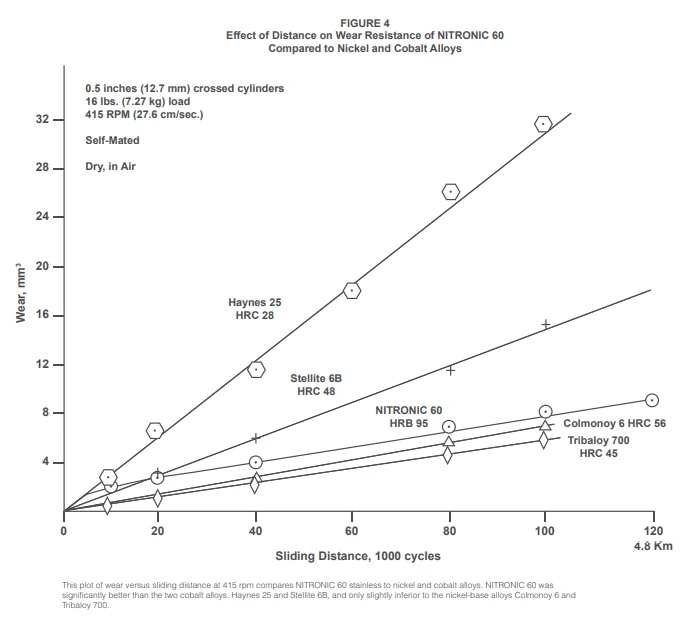
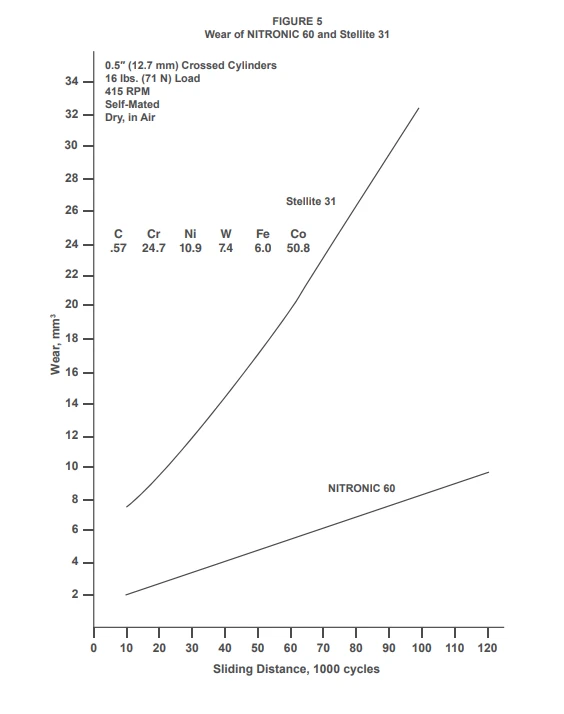
Elevated Temperature Wear
The elevated temperature wear resistance of N60 is excellent despite the alloy’s relatively low hardness when compared with cobalt and nickel-base wear alloys. To minimize wear, NITRONIC 60 relies on a thin adherent oxide film and a high strain-hardening capacity to support the film. N60 also performs well in metal-to-metal wear in nominally inert atmospheres.
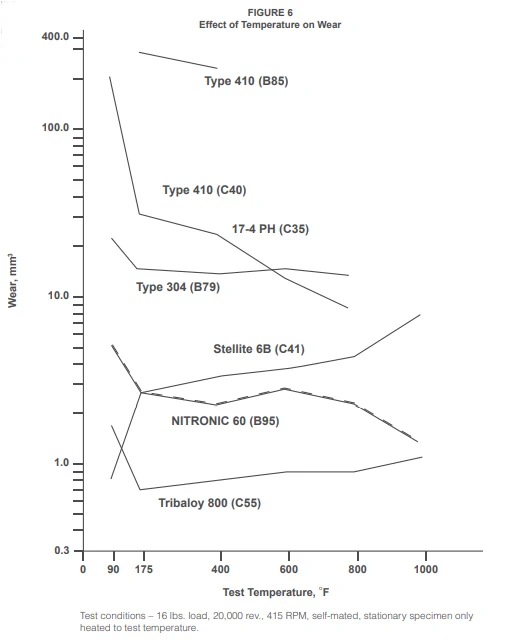
Fretting Wear
Fretting wear is caused by high loads at very small slip amplitudes (40 µm), such as found in vibrating components. N60 exhibits fretting wear at 1112 °F (600 °C) similar to 718 which has been found to be one of the most fretting resistant alloys at this temperature.
Cavitation Erosion
Cavitation erosion resistance of N60 is superior to the austenitic stainless steels as well as high strength duplex (ferritic austenitic) stainless steels. It approaches the cobalt-base alloys which are considered among the most cavitation resistant alloys available.
N60 stainless steel has proven highly successful for wear rings in vertical centrifugal pumps. The combination of N60 and N50 stainless steel steels have replaced some cobalt wear alloys as they offer outstanding wear and corrosion protection. N60 stainless steel has also been cased up to 8550 lbs for water pump impellers where CA-6NM has proven inadequate. It is anticipated that the excellent galling resistance, cavitation erosion resistance, and good castability of N60 stainless steel will make it an ideal choice for turbine runners, especially with integral case wear rings.
Corrosion Resistance
The general corrosion resistance of N60 stainless steel falls between that of Types 304 and 316. However, experience shows that in a wear system, a galling or seizing failure occurs first. Followed by dimensional loss due to wear and finally corrosion. Galling and wear must be the first concerns of the design engineer. Although the general corrosion resistance of N60 is not quite as good as Type 316, it does offer better chloride pitting resistance, stress corrosion cracking resistance, and crevice corrosion resistance. Corrosion tests are not normally performed on N60 HS.
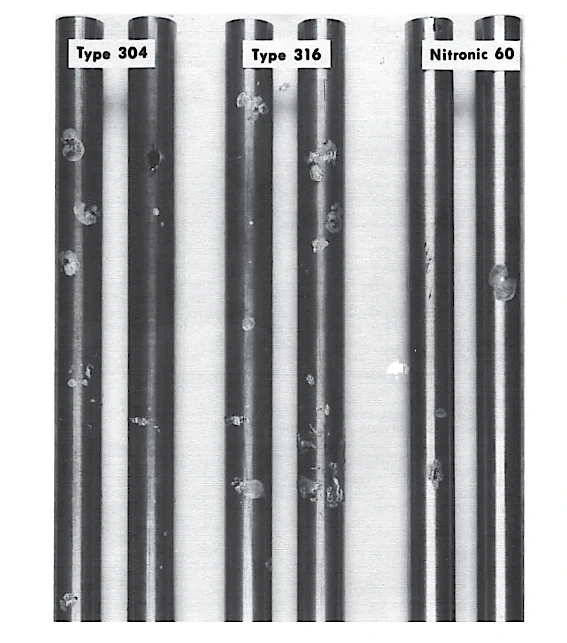
Seawater Corrosion Resistance
When exposed for 6 months in quiet seawater at ambient temperature, N60 stainless steel exhibited far better crevice corrosion resistance than Type 304 and slightly better resistance than Type 316 stainless steels. These tests were run on duplicate specimens and all grades were exposed simultaneously.
High Strength (HS) Bar Properties
N60 stainless steel bars are also available in a high strength condition attained by special cold processing techniques. Because high strength is produced by cold working, hot forging or welding operations cannot be performed on this material without loss of strength. Aqueous corrosion resistance may also be lessened to varying degrees, depending upon the environment.
Welding
Nitronic® 60 stainless steel is readily welded using conventional joining processes. Autogenous welds made using the Gas Tungsten-Arc process are sound, with wear characteristics approximating those of the unwelded base metal. Heavy weld deposits made using the Gas Metal-Arc process and the matching weld filler are also sound with tensile strengths slightly above those of the unwelded base metal. Wear properties are near yet slightly below those of the base metal.
The use of Nitronic® 60 stainless steel for weld overlay on most other stainless steels and certain carbon steels develops sound deposits having properties about equal to that of an all weld deposit.
The American Welding Society has included Nitronic 60W bare wire in AWS A5.9 as ER 218 alloy.
General Welding
Nitronic® 60 is an austenitic stainless steel and can be handled in the weld shop like AISI 304 and 316. No preheat or post-weld heat treatments are considered necessary other than the normal stress relief used in heavy fabrication. The nature of Nitronic® 60 applications suggests that most uses would occur in the as-welded condition except where corrosion resistance is a consideration.
Fillerless fusion welds (autogenous) have been made using the gas tungsten arc process. The STA welds are free from cracking and have galling and cavitation resistance similar to the unwelded base metal. Heavy weld deposits made using the gas metal arc process are sound and exhibit higher strength than the unwelded base metal. The metal-to-metal wear resistance of the GMA welds is slightly lower than the base metal heat resistance. Detailed test results of weld metal properties are listed in Table 5 of the Nitronic® 60 product data bulletin.
Although no first-hand dissimilar weld data is available from our Armco welding laboratories, past experience suggests that Nitronic® 60 can be welded to both AISI 316 and 400 series stainless steels with Type 309 welding wire. The usual handling procedure for welding 400 series alloys would probably dictate fabricating sequence in many cases, but most specific applications require individual fabrication plans.
Repair Welding of N60 Castings
A simulated repair weld has been completed on a 4”x 9”x 9” section of as-cast Nitronic® 60. The welded joint was prepared by manually air-carbon-arc gouging a “V” groove and then grinding to remove carbon deposits. Developmental AMAW electrodes were used under the following conditions:
Welding current | 130-140 Amps |
---|---|
Welding Voltage | 26-28 |
Travel Speed | About 8-10”/min. |
Preheat Temp. | Room Temp |
Interpass Temp. | 300°F Max. |
Post Weld Heat Treat | None |
Electrode Diameter | 5/32” |
Groove Depth | 1 to 1.25” |
After cooling to room temperature, the weldment was sectioned in several locations and dye penetrant inspected. No evidence of cracking was observed in any section.
N60 Weld Overlay of Wrought and Cast Steels
Bare wire, .062” diameter, is the most common size available for use with any filler added process that uses an inert gas shield like Gas Metal Arc, Gas Tungsten Arc, Plasma Arc, Laser, etc. The Gas Metal Arc Process may be used in any one of three modes for overlay welding; spray arc, shorting arc, and pulse arc.
While the use of any inert gas shielded process is considered applicable for deposition, the metallurgical considerations pose a serious limitation. For example, the Gas Tungsten Arc Process with a cold wire feed is not recommended because of the inherent high base dilution effects that make it virtually impossible to get a sound overlay, even with sub layer practices. The hot wire version of the Gas Tungsten Arc Process may work if properly controlled. Very high arc current to hot wire current ratios would have to be used to get a low base dilution (should be 25% or less). The intergranular corrosion resistance of Nitronic® 60 as a weld overlay on AISI 304 appears satisfactory even in the as deposited condition.
References
Link to Electralloy's datasheet/brochure on Nitronic® 60Nitronic® is a registered trademark of Cleveland-Cliffs Steel Corp, successor to AK Steel.
Data referring to mechanical properties and chemical analyses are the result of tests performed on specimens obtained from specific locations of the products in accordance with prescribed sampling procedures; any warranty thereof is limited to the values obtained at such locations and by such procedures. There is no warranty with respect to values of the materials at other locations.